The liquid pharmaceutical manufacturing industry is constantly evolving, shaped by critical priorities – reducing contamination risks, meeting stringent regulatory requirements, controlling costs, promoting sustainability, accelerating production timelines, and achieving operational excellence across both large-scale and small-batch sterile filling operations.
To address these challenges, manufacturers must adopt strategies that balance the often competing goals of efficiency, adaptability, and an uncompromising commitment to safety.
Four proven strategies
At Syntegon, we provide innovative, reliable solutions designed to meet the ever-changing demands of the industry—today and tomorrow. Drawing on our extensive expertise, we’ve identified four proven strategies that are especially effective in empowering liquid pharmaceutical manufacturers and CMOs to address their most pressing needs –
-
Accelerate project timelines with integrated, single-source solutions.
-
Reduce costs with compact, space-efficient equipment.
-
Streamline workflows using Ready-to-Use (RTU) containers.
-
Boost efficiency and eliminate human error through automation.
These strategies work in harmony, complementing and reinforcing each other. Together, they provide both flexibility and outstanding yields to achieve productivity and efficiency without sacrificing quality. By adopting these approaches, manufacturers can confidently tackle the challenges of modern pharmaceutical production while upholding the highest standards of product safety.
1. Single-source solutions – accelerate project timelines
Single-source solutions significantly enhance efficiency in liquid pharmaceutical manufacturing by integrating various systems into a unified package. This approach streamlines workflows, minimizes maintenance issues, and improves aseptic production safety and efficiency. Partnering with a single-source provider simplifies the entire equipment implementation process, from planning to approval, ensuring seamless compatibility across all components.
A single-source solution, complete with integrated factory acceptance testing, helps eliminate delays and reduces multi-vendor management, accelerating production line launches. This allows manufacturers to bring products to market faster and more efficiently. The streamlined approach also enhances operational reliability by eliminating communication issues and technical problems often associated with multiple vendors, resulting in better service, support, and faster troubleshooting, ultimately saving time and reducing downtime.
2. Compact equipment – reducing costs
Boosting efficiency in pharmaceutical manufacturing can be as straightforward as adopting compact equipment. In cleanroom environments, where every inch of space matters, bulky traditional equipment often limits productivity. Compact, intelligently designed, and well-integrated systems offer the same high-performance capabilities while taking up far less space, maximizing the facility’s operational potential.
By reducing equipment size, manufacturers can lower both capital and operational costs. The additional freed-up space can be repurposed for other productive activities, such as scaling up production lines or implementing new processes. This approach enhances adaptability and resource efficiency, allowing facilities to meet evolving demands without the need for costly expansions.
Bulky Air Handling Systems. One of the greatest challenges in designing compact isolators is managing the air handling systems needed to regulate temperature, humidity, and airflow. Traditional isolators often relied on large, external air handling units installed on technical floors above filling systems. These setups take up a lot of space and require complex piping infrastructures, making the overall design cumbersome and inefficient.
Syntegon’s innovative ‘In-air’ isolators address the problem by integrating advanced air handling technology into the isolator’s plenum. By eliminating the need for bulky external air handling units and their associated piping, ‘In-air’ isolators free up valuable space on technical floors and reduce installation complexity and costs.
The system pulls air from the surrounding class C cleanroom and exhausts it back into the same space, maintaining a neutral air balance without interfering with the cleanroom’s ventilation system. Additionally, since the air required for the isolator is sourced directly from the controlled cleanroom environment, there’s no need to pull in and treat external air, resulting in significant energy savings.
Originally developed for small-batch filling systems, such as Syntegon’s Versynta FFP (Flexible Filling Platform) and Versynta microBatch, this integrated air-handling solution is now available for large-scale production equipment. It offers a more compact, energy-efficient, and cost-effective approach to air handling in pharmaceutical manufacturing. All of Syntegon’s filling lines also feature a laminar flow-optimized design to make sure that the airflow can reach the containers and flow around them without obstruction.
3. Ready-to-use (RTU) containers – streamlining workflow
The growing adoption of ready-to-use (RTU) containers has been a game-changer for liquid pharmaceutical manufacturing. These pre-cleaned, pre-sterilized containers eliminate several production steps, significantly reducing time, labor, and space demands. For pharmaceutical manufacturers, RTU containers streamline workflows, lower the total cost of ownership, and offer greater operational flexibility. They are particularly well-suited for small to midscale-batch production, for volumes up to 200 to 400 containers per minute.
Tasks like cleaning, siliconization, and sterilization—traditionally handled in-house—are outsourced to specialized packaging suppliers. These suppliers bring expertise to the table, ensuring all processes are fully qualified, validated, and compliant with global standards. Containers are delivered certified with controlled endotoxin, germ, and particle levels. For pre-sterilized syringe systems, this includes precise siliconization as well.
RTU containers not only simplify manufacturing workflows but also reduce space, media and energy consumption. By arriving pre-prepared, they eliminate the need for in-house cleaning and sterilization—additional process steps that require flawless function. This enhances product safety while increasing overall process efficiency. For manufacturers focused on small-batch production, RTU containers offer added flexibility, allowing faster transitions between production runs, minimizing downtime, and enabling rapid responses to market demands.
4. Automation and digitalization – boost efficiency and eliminate human error
Automation is one of the most transformative approaches to enhancing efficiency and safety in liquid pharmaceutical manufacturing. It enhances productivity, improves quality, and addresses workforce challenges across various industries, but its impact is especially transformative in the pharmaceutical sector.
The need for safety, contamination prevention, precision, consistency, traceability, and the prevention of the loss of any valuable product has made automation an indispensable tool for achieving the highest standards in pharmaceutical filling operations.
The rapid adoption of robotics. Human intervention remains the leading cause of pharmaceutical contamination. Implementing automation is critical to minimizing or eliminating these risks. As early as 2004, the FDA emphasized that “the design of equipment used in aseptic processing should limit the number and complexity of aseptic interventions by personnel.” Furthermore, the FDA highlights that “automation of other process steps, including the use of technologies such as robotics, can further reduce risk to the product.”
The recent update to Annex 1 of the Good Manufacturing Practice (GMP) guidelines has further propelled the adoption of automation in the pharmaceutical industry. Annex 1, which focuses on sterile manufacturing processes, places a stronger emphasis on reducing human intervention and implementing appropriate technologies. In the long run, aseptic filling will evolve from human-centered to fully automated production with the use of appropriate technologies.
The transformation in aseptic filling operations is already well underway, driven by advancements in automation, particularly robotics. These innovations have redefined the role of isolators by significantly reducing or even eliminating the need for glove ports—long considered a weak point in maintaining sterility. Traditional isolators rely on glove ports for human intervention, but each use carries a risk of contamination, whether through breaches in sterility, particulate matter, or microbial exposure. Additionally, the maintenance and sterilization of gloves are both time-consuming and labor-intensive, further complicating the process.
Robotics have emerged as a game-changer in this space. For instance, using robotic arms to transfer containers within the isolator to the filling station and onward to the stoppering (and crimping, as needed) stations substantially minimizes contamination risks. Robots not only reduce the need for multiple format parts but also eliminate glass-to-glass contact entirely. Furthermore, the integration of 100% in-process control (IPC) during filling minimizes product loss and ensures the precise filling of nearly every milliliter of high-quality product. This level of precision and efficiency underscores the immense potential of robotics and more broadly automation in transforming aseptic filling operations.
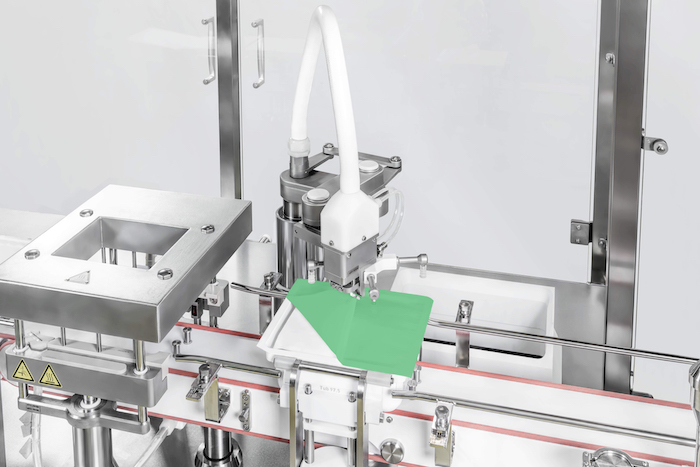
In the early days of robotics, two decades ago, simple machines were primarily used for repetitive, routine tasks, where precision and consistency were key. Today, robots have evolved far beyond these basic functions and are now capable of performing highly sophisticated operations in fully automated environments. Modern robotic systems are perfectly suited for operation within isolators, maintaining a sterile and controlled environment. Unlike human operators, these machines can work tirelessly without the need for breaks, significantly boosting efficiency and productivity.
The capabilities of robots now match—and often exceed—what humans can achieve.
-
Dexterity – Modern six-axis robotic arms deliver remarkable precision and versatility, with 360-degree mobility and exceptional fine motor control. Their advanced dexterity allows them to handle intricate and delicate tasks once thought possible only for human hands.
-
Precise remote handling – Syntegon’s advanced robotic filler features remote control of the robotic arm for troubleshooting or other manual tasks without opening the isolator. This functionality allows operators to perform unanticipated interventions without the need for glove ports, enhancing process safety.
-
Advanced inline inspection – Advanced inline inspection enables continuous quality inspection and real-time feedback for precise operational adjustments, exceptional accuracy and consistency in tasks like verifying stopper placement and monitoring crimp quality
-
Data collection and analytics – Digitalization is now integral to data-driven operations. The collection and analysis of data during workflows, enables better decision-making, improved efficiency, traceability, and predictive maintenance to avoid downtime.
Automated settle plate changer. A compelling example of how robotics enhances uptime and process reliability is the automation of settle plate handling. According to the EU GMP Annex 1 guideline, settle plates must be exposed to cleanroom air for no more than 4 hours, requiring frequent manual interventions.
Syntegon has introduced the SPC (Settle Plate Changer) 1000, an advanced robotic handling unit that extends the interval between manual interventions to 24 hours. This innovation, available on new equipment or as a retrofit, reduces contamination risks, ensures regulatory compliance, and maximizes equipment availability, typically resulting in an additional 125 hours of uptime per year and increased production efficiency.
Comprehensive strategy
The latest generation of fill/finish systems combines all four strategies into a unified, comprehensive approach. These systems accelerate project timelines with integrated, single-source solutions while reducing costs through compact, space-efficient equipment. Numerous equipment models are optimized to leverage ready-to-use (RTU) containers, boosting overall efficiency. Additionally, the incorporation of robotics streamlines operations and eliminates human error, enhancing safety, reliability, and performance.
The Syntegon Versynta systems embody the industry’s shift toward comprehensive solutions for pharmaceutical fill/finish processes. The Versynta FFP (Flexible Filling Platform) is a modular, high-volume system designed for ready-to-use (RTU) containers. Featuring pre-developed, pre-tested modules, it delivers outputs of up to 3,600 units per hour with 100% in-process check-weighing and seamless isolator integration.
For small-batch production, the Versynta microBatch production cell offers a compact, fully automated solution. Designed for flexibility, it handles up to 500 containers per hour, accommodating syringes, cartridges, and vials made of glass or plastic with minimal product loss. Its space-efficient design (3.5m x 2m x 3m) allows easy integration into existing production environments.
Balancing efficiency and safety
Pharmaceutical manufacturers must prioritize both efficiency and safety—there’s no room for compromise. Solutions such as single-source partnerships, compact equipment, ready-to-use (RTU) containers, and advanced automation offer a powerful way to achieve this balance. By embracing these strategies, manufacturers can enhance competitiveness, optimize operations, and bring high-quality products to market more quickly and reliably.