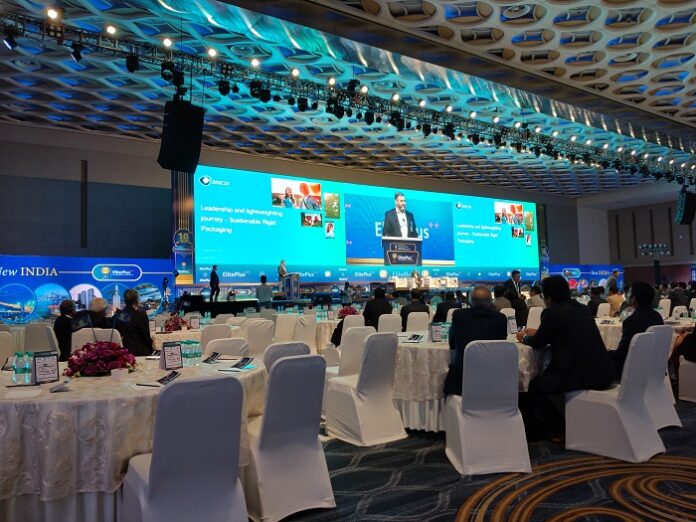
At the 10th Injection, Blow Molding and PET Global Summit held in Mumbai, Graeme Hood, director of R&D at Amcor Global Rigid Packaging Solutions, outlined the company’s latest strides in sustainable rigid packaging. Speaking to an industry audience, Hood emphasized the twin pillars driving Amcor’s innovation agenda—lightweighting and circularity.
Introducing the Amcor delegation present at the event, Hood confirmed the company’s recent integration with Berry Global, describing it as a transformational move. “With this merger, we are a single company offering unmatched global scale, capabilities, and innovation,” he said. The combined group operates more than 400 manufacturing sites — nine in India — across 40 countries, employing over 70,000 people worldwide.
“This combination brings together the best of both worlds,” Hood noted. “Amcor’s legacy in flexible packaging and Berry’s leadership in rigid packaging solutions allow us to create comprehensive, high-performance offerings that can support your growth not just in India, but globally.”
Amcor has set ambitious sustainability goals, including achieving 30% circular polymer content across its packaging by 2030. Hood said the strategy involves widespread adoption of monomaterial packaging, improved recyclability, and continued lightweighting of components. “We are transforming not just our products, but the industry itself. This is how we create long-term value while meeting environmental expectations.”
He highlighted two lightweight closures that have been developed and commercially validated for the Indian market: a 2.05g 1881 closure for carbonated soft drinks and a single-piece GE 3041 closure weighing 1.65g. These closures have been subjected to stringent testing under high temperature and pressure conditions, with Amcor closures outperforming rival products in 120-hour stress tests. “This level of performance matters in India, where products face diverse climate and logistical conditions,” Hood said.
On the bottle front, Hood presented Amcor’s innovations in hot-fill PET base technologies. The company’s PowerFlex, PowerStrap and forthcoming PowerPost bases offer up to 25% weight reduction compared to conventional designs. “Using AI, we ran more than 80 million bottle base design simulations in just one weekend,” Hood explained. “This level of digital R&D enables us to deliver lighter bottles that still meet vacuum resistance and performance expectations.”
A significant part of his presentation was dedicated to dispensing solutions. Hood traced the evolution from Amcor’s legacy Magic Star pump—a 12-part assembly—to the streamlined Magic One, now comprising just five recyclable polyurethane components. “Magic One offers flexibility and sustainability in one package. It works across multiple viscosities and dosages, and it’s designed for recyclability from the start,” he said.
He introduced the Echo Line trigger pump; a fully recyclable design made of 97.5% polyethylene. Capable of incorporating up to 70% PCR content and tested for over 5,000 strokes, the Echo Line pump is targeted at home and personal care products. “With dispensing, we’re moving from complexity to elegant, eco-friendly simplicity,” he added.
“These are not small steps,” Hood concluded. “They’re part of a broader strategy to bring science, sustainability and scale together. At Amcor, we’re not just adapting to change—we’re accelerating the possible.”