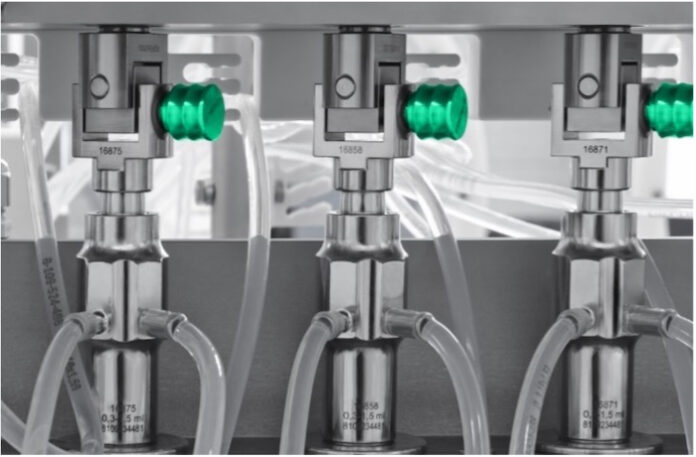
Product piracy is not only widespread in the world of media and fashion. In mechanical and plant engineering, too, counterfeit products have long since ceased to be a marginal phenomenon and have rather become a common, high-risk practice. However, cheap copies of critical spare and format parts rarely lead to the desired cost savings. On the contrary – companies in the pharmaceutical industry risk product contamination, faulty production, loss of quality, exclusion of warranty, and machine downtime due to counterfeit parts. Only with original quality components – whether for new machines or retrofits – can maintenance and production costs be kept low and consumer safety ensured.
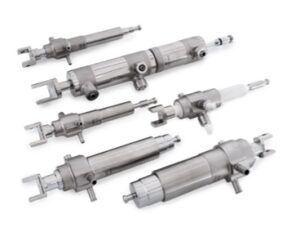
According to a survey conducted by German statistics portal Statista among 105 members of the German engineering association VDMA, the total damage caused by counterfeit mechanical engineering parts in Germany in 2024 is estimated at 4.1 billion euros. Although this may sound like a large sum at first, it shows a positive development compared to previous figures. In 2022, it was 72% of VDMA members stating that they were affected by illegal replicas, copies, or other counterfeits of their spare and format parts. While this figure is currently lower – 46% – it is still a worrying number .
Counterfeit products – only cheaper at first glance
The continued high demand for counterfeit machine parts stems from a fundamental fallacy that companies, including those in the pharmaceutical industry, often succumb to. If, for example, a format part of a packaging machine is defective, some manufacturers fall back on a cheaper copy instead of sourcing the original quality component. However, this decision only leads to short-term financial benefits. In the long term, the opposite occurs – the counterfeit format part often significantly increases the likelihood of damages and production errors and may lead to lengthy machine downtimes and high costs.
Product contamination due to counterfeit format parts
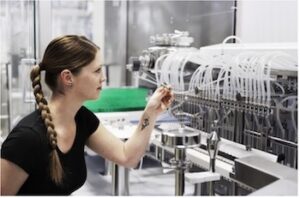
Photo Syntegon
One particularly dangerous effect is the increased risk of contamination, as this directly endangers the health of consumers. Counterfeit components are often made from inferior materials and can cause contamination, especially in sectors with high hygiene requirements such as the pharmaceutical industry. Particles can detach from the surface of the component and contaminate the product. This is particularly the case with critical product-contact format parts, such as auger dosing systems, rotary valve pumps or filling needles. In addition, the inferior material may not be compatible with the cleaning agent, preventing proper cleaning. If the contaminated products reach the market, companies risk global recalls that not only result in serious financial losses, but also cause lasting damage to the customers’ trust in the brand.
Product counterfeiting as cause of defects and faulty production
Deviating geometries of counterfeit spare and format parts can also cause expensive damage. When manufacturers decide to save on a supposedly non-critical component – for example, the individual gears of the conveyor belt in a packaging line – they run the risk of the counterfeit part getting caught in the drive shaft of the conveyor belt or not being able to withstand the mechanical stresses during production and becoming deformed or breaking off. The result – the entire conveyor belt is damaged and has to be replaced, causing unforeseen machine downtime. The manufacturer incurs repair costs that far exceed the purchase price of the counterfeit format part. Faulty production may also result in higher costs down the line. Faulty counterfeit parts can lead to overdosing or poor sealing quality – and therefore to products that do not meet the required specifications.
Warranty exclusion and long-term system availability
Pharmaceutical manufacturers must bear these additional costs themselves, as manufacturers of counterfeit products accept no liability for financial losses. Furthermore, they mostly do not guarantee reliable parts availability for years in advance. If the counterfeit spare part is damaged, plant manufacturers and pharmaceutical producers cannot count on a speedy replacement.
In addition, manufacturing companies cannot rely on counterfeit products meeting the high standards of consumer protection and machinery directives. In contrast, original manufacturers guarantee that their spare and format parts meet the highest quality standards and are certified in accordance with all relevant regulations. They also guarantee that their parts are compatible with their machines and provide comprehensive documentation and operating instructions to ensure an efficient and safe production process. They are also legally obliged to ensure a ten-year parts and service availability to enable long-term strategic planning.
Preventive approach for optimum efficiency
Close cooperation with machine and system manufacturers is also worthwhile as a preventative measure and not only when a component is defective. Their experts have many years of technical expertise and industry knowledge under their belt. They can therefore provide pharmaceutical manufacturers with comprehensive advice and support to avoid machine and production errors and reduce future complaints to a minimum.
Efficient modernization for future-proof production
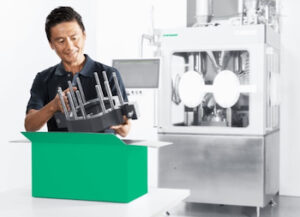
When it comes to modernization, pharmaceutical manufacturers are on the safe side when they work with the manufacturers of their process and packaging machines such as Syntegon. This includes switching to sustainable packaging and production processes. To ensure a smooth transition, Syntegon’s experts carry out extensive analyses as well as machine and material tests in in-house test laboratories to determine the right solution for every product requirement, whether that may be a retrofit or a new machine. They also provide support during commissioning and train operating personnel to ensure smooth production processes. During operation, pharmaceutical manufacturers have access to comprehensive service agreements and digital monitoring solutions, which provide the data needed for continuous optimization of process parameters – always with the aim of ensuring long-term efficiency.
Albert Qorraj, is director of Product Management Parts & Consumables at Syntegon