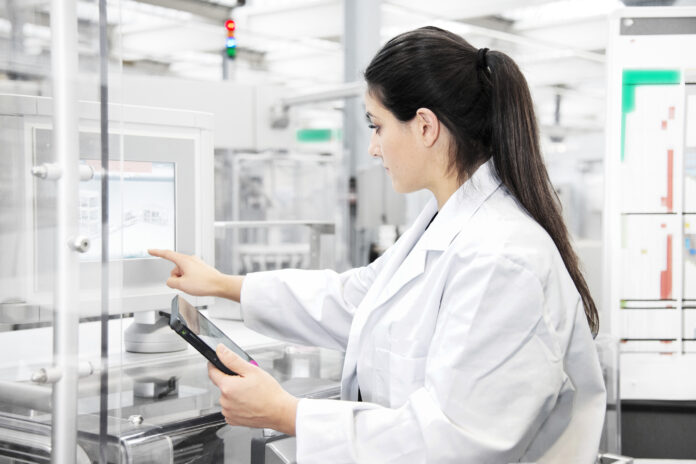
Just like we human beings, production equipment also needs a health check-up every now and then. However, if a packaging or processing line is no longer running at full capacity, a brief consultation with the general practitioner isn’t enough. What food and pharmaceutical producers need to keep their lines going at high output and with good product quality for decades is a thorough audit, performed by a team of specialist ‘doctors’. Their mission is to identify the underlying issues and prescribe the right treatment to optimize performance and processes.
Whether it is the output or scrap rate, set-up or handling time – packaging and processing lines have many areas where subtle problems can hide. Even a line that has been running seemingly efficient for years will eventually see a loss in performance. If this takes place very gradually, it is hard to notice until the initial and the current output is compared. But once a problem is recognized, how is the manufacturer to identify these hidden issues without disassembling the entire line?
Technical audit
The answer is called a ‘technical audit’ – a common service offered by many providers. However, there is a key difference between a standard technical audit and one conducted by a team of experts from the OEM (original equipment manufacturer). Just like in human healthcare, a general practitioner is always a good starting point. But when you need to look deeper into the causes of a health issue, you will likely need to meet with several individual doctors, each of whom examines one specific issue. As a result, it can take weeks, months, or even years to get to the root cause of your symptoms. However, machines have a clear advantage over human beings — if they are treated correctly, they can have immediate access to an entire team of specialists with decades of experience in all fields — ophthalmologists, orthopedists, and cardiologists, and psychologists.
Before the examination – Decision to invest
Imagine, for example, a flow wrapping line for cookies. The operations and maintenance teams have been successfully working with the line for five years, and the cookie producer is generally very satisfied with the line’s overall production rates. However, the quality group recently compared the line’s current scrap rates with those when it was originally installed and found that the waste rate has grown. The line must have an issue somewhere. A pharmaceutical vaccine producer might encounter a similar situation. The machine’s transport system is working at a slower pace than usual, and the output has manufacturing declined. In both cases, the reasons for the discrepancies are not immediately obvious – so both the cookie producer and the pharmaceutical manufacturer decide to invest in a technical audit.

Before the actual technical audit can begin, it is important to understand the customer’s perspective. A subset of the technical audit team will interview the customer to discuss the major pain points affecting the ‘patient’ (that is, the machine or line) with the experts from the customer side.
This discussion results in a list of expectations, goals, and possibly what to look for to improve the packaging or processing line’s overall efficiency. At this point, the technical audit team will determine the best course of action and define the next steps in the process. During these steps, the service provider and customer must be completely aligned with regard to desired KPIs and metrics; that is, how success is measured. This will be important to provide the customer with solutions that correlate directly to the final proposal’s desired improvements.
The check-up – Identifying subtle issues
Performing an in-depth audit on an entire line takes time. Obvious problems are easy to see, and solutions to them are usually self-evident. Identifying subtle issues, with several permutations of variables, requires a more thoughtful approach. Critical to any analysis is to ensure that the data recorded is accurate. To that end, interdisciplinary experts make sure the line runs in a stable state before any data recording. All obvious issues are corrected immediately. Once the line is running smoothly, the audit team can begin collecting data. They check and record the packaging or processing line’s performance in various categories, such as output, scrap rate, or overall speed.
The audit must be performed on the product most important to the customer. This is determined in the initial team meeting with the customer and normally defined as the product where the customer experiences the biggest shortfall in profit or performance. It can also be defined as the line where efficiency gains are of prime importance. While auditors are collecting data, the technical team is analyzing line stoppages and scrap generators.
The experts examine each process step within the line, retrieve the data, and compile it in a comprehensive overview. Based on this overview, the ‘doctors’ can now assess their patient’s condition in detail and draw some initial conclusions. This in-depth analysis shows where the line is running efficiently and pinpoints areas of concern. But most importantly, the experts can see at which points the results differ from the expected performance.
If, for instance, excessive rejects and stoppages occur at the wrapper, a common assumption by the customer is that some machine tuning or a few new components will restore the line’s usual rates. However, as mentioned previously, the technical audit is meant to uncover hard to find issues. The technical team identifies that the real issue is product distribution, product infeed, or other upstream parts of the process. The data on the pharmaceutical company’s vaccine filling line, in turn, might reveal problems with the transport system, which calls for a technical update.
At the same time, the team may identify issues in handovers of the line between shifts. In this case, other specialists can offer operator training as a suitable remedy. The expert technical team identifies the root cause while the audit team quantifies and correlates the impact the issues have on the system.
Treatment in progress
Once the previously hidden issues have been diagnosed, the team can make treatment recommendations. The equipment and service supplier creates a quotation and a roadmap for improvement measures with estimated improvements in the customer KPIs as designated at the initial meeting. Before the plan is put into action, a final meeting is convened with the original customer stakeholders to discuss the team findings, assumptions, conclusions, and solutions.
The customer, in turn, may prioritize the most important measures and approves the overall process. The treatment plan differs from patient to patient and might consist of measures such as new spare parts, modernizations, or even operator training. Before the project is completed, the audit team checks all implemented measures and compare them with the KPIs previously defined together with the customer.
Medical aftercare is just as important for packaging and processing lines as it is for human beings. Whichever treatment plan is chosen, it is crucial to monitor the success of each measure. Consequently, the audit team revisits the patient after a certain time (usually a year after implementing the agreed-upon steps). Together with the field service team, they check whether the measures have produced the desired results and issue a service report if they have any suggestions for further optimization.
Significant savings due to increased line efficiency
Above all, service providers and customers focus on the concrete results — have the measures taken reduced scrap, increased output and performance, and have they led to better handovers between different shifts or even individual staff members? After all, a technical audit, combined with the subsequent measures, is a cost-intensive undertaking that should provide a valuable investment return. The aftercare shows that, just like with people, intensive check-ups provided by different doctors take time and cost money – but in the end, well-being is increased. And in the case of packaging or processing machines, they not only prolong the lifetime of the equipment. They also result in significant savings due to increased line output and efficiency.
Author – Kurt Sykes, business development manager – Customer Service at Syntegon Technology