
When a leading global collagenase manufacturer wants to renew and optimize a system at the heart of its production, technical expertise and engineering competence is paramount. Moreover, cooperation within the project team needs to be well organized. Nordmark and Pharmatec, a subsidiary of Syntegon, have shown how this helps to master even unexpected challenges during the construction of a new filtration and concentration system for collagenase.
With 650 employees, Nordmark Pharma, based in Uetersen, Germany, is not one of the world’s largest pharmaceutical companies. Nevertheless, the owner-run, fully integrated medium-sized company has a leading position in the development and production of biopharmaceutical active ingredients and pharmaceuticals. Nordmark is the global market leader in the production of collagenase and as a supplier of collagenase for tissue dissociation and cell isolation. Collagenase is used for enzymatic wound cleansing and in research for the isolation of cells and tissue. Nordmark produces both collagenase-containing sterile ointments for burn victims and highly purified collagenase in various degrees of purity for research purposes and clinical facilities.

Photo Syntegon
In 2019, Nordmark decided to replace its system for filtration and concentration of collagenase with a more state-of-the-art solution. It was clear that the design and construction of the highly specialized equipment would require a partner with in-depth expertise, as well as the ability to develop and implement a customized solution for the GMP area. Pharmatec, a subsidiary of Syntegon, was already well known to Nordmark at that time. “Right next door to the filtration system, we have two further Pharmatec plants we are very satisfied with,” says Steffen Lehmann, Team Lead Engineering API Production at Nordmark. “Hence, the decision to cooperate again was obvious for us.”
Completely renewed for the highest standards
The existing production equipment for collagenase filtration and concentration was past its prime, especially regarding plant availability and production supply assurance. Meeting current hygiene and safety standards was complicated and cumbersome. The automation of production processes was also only possible to a very limited extent. The task for Syntegon consisted in optimizing these aspects during the design and construction of the new plant. At the same time, the basic production process and mode of operation were to be maintained. “We didn’t want to replace our old system with something more or less the same. We wanted to upgrade our equipment to the current state of science and technology,” says Lehmann.
Collagenase is obtained by fermentation in an upstream step. It is then transferred to the new equipment, where it is purified and concentrated in two tanks via filtration. All components are accessible quickly and with few tools, allowing maintenance work to be carried out with minimal effort. Moreover, the system offers many possibilities for customized process automation. Cleaning, for example, is also performed automatically – thanks to a new, integrated CIP concept, compliance with current hygiene standards is now an integral part of the production process. In addition, the new system features more powerful and standardized measuring technology. Operation is easy to learn, while immediately usable data is provided on production and equipment status. The system is connected to Nordmark’s also renewed process control to evaluate the data and facilitate equipment monitoring.
Support right from the start
The cooperation between Pharmatec and Nordmark began in a somewhat unusual fashion – since the filtration system was not only to be replaced but also required thorough optimization, Nordmark had prepared an extensive list of specifications. In addition, the new equipment was to work according to the existing process, for which no documentation was available. “The resulting complexities prompted us to get the support of experienced experts at an early stage,” says Lehmann. Pharmatec therefore already advised Nordmark during the first planning phase. The engineers analyzed all requirements and drew up a comprehensive project plan.
“We were able to get an accurate idea of the time frame and costs before the project had even started, all thanks to the expertise and many years of experience of Syntegon’s specialists,” says Steffen Lehmann. By choosing Syntegon as a project partner, Nordmark also made sure it would be prepared for any future modifications. The company and Steffen Lehmann know from experience, “Pharmatec not only provides us with a suitable system, but also with the ideal qualification documentation.”
Engineering-to-order despite bottlenecks
Successful planning was followed by the design phase. The collagenase filtration and concentration process is highly specialized and required an individually tailored solution. “In fact, there was no ready-made design on the market that would have met all our requirements,” Lehmann recalls. Moreover, the available space was also clearly defined; the dimensions of the previous system were not to be exceeded to avoid the need for structural changes and a lengthy production stop.
Of course, an interruption of routine operations could not be completely avoided. It was, however, limited to a precisely scheduled and tightly timed step in the project plan – which suddenly threatened to be delayed in 2022 due to bottlenecks in the global supply chains. A supplier was unable to provide components for important control elements within the planned time frame. Once again, Syntegon proved to be the right project partner for Nordmark, as the project team immediately created a comprehensive plan of action and took up matters with the supplier. This solution-oriented approach paid off, “After the initial shock and a one-time adjustment of the schedule, there were no further delays,” says Lehmann.
Fast qualification
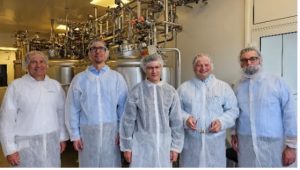
Photo Syntegon
The combination of detailed planning, good project management, sound expertise, and flexibility in the face of disruptions brought the project to a successful close for both partners. The qualification of the system, which is usually a lengthy process for such a complex technology, was completed much faster than expected. This was followed by an equally short optimization phase, where the system’s automated processes were adjusted according to the customer’s individual requirements. “It was almost too good to be true,” says Steffen Lehmann. The system started routine production in March 2023. Nordmark sees itself well positioned for upcoming challenges – “Both the new system with its usual high quality and the maintenance service from Pharmatec make us more future-proof,” Lehmann summarizes.