The Chemical Business division of UFlex manufactures inks, adhesives, and coatings primarily for the packaging industry. At the recent PlastIndia show in New Delhi, the division promoted its water-based inks for flexible packaging and corrugation, pharma inks, and LED curing inks.
“UFlex has taken the initiative to provide sustainable, green, and cost-effective solutions. After Covid, the demand for packaged food has gone up and everybody is looking for a unit pack. We are selling more than 50,000 tons of inks and adhesives every year, probably because we are the largest ink manufacturer here. At the same time, we are investing substantially in water-based technologies, particularly LED technologies. LED inks are the primary energy savers for offset and energy saving is one of our sustainable initiatives,” said Rajesh Srivastava, senior vice-president of the Chemicals Business at UFlex.
Inks are a very expensive component for any packaging, and when it comes to the efficiencies, speeds, and costs reductions, he explained. “We offer state-of-the-art products that reduce overall ink consumption. While the brand owners are pushing for competitive prices, the raw material prices are going up. Hence, we have to offer solutions where flexible packaging converters can save either on the solvent cost or overall ink consumption. We offer a total solution-based approach where the inks, adhesives, cylinders, and the overall machine can play a significant role in combination,” he said.
UFlex manufactures its range of toluene-free sustainable inks at two plants – in Noida Sector 57 starting in 1994, and the Jammu plant beginning in 2008. The Jammu plant was initially aimed to support the Jammu UFlex divisions but has now started selling to outside customers as well.
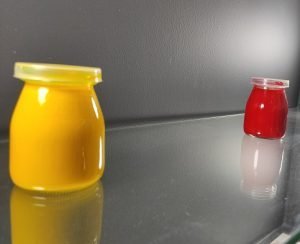
“We sell to many customers and distributors based in Hyderabad, Bengaluru, and other Southern cities. We are dealing with more than 300 converters, and more than 100 distributors, which include several global and Indian clients such as Constantia Flexibles. If you take 95 of India’s top converters, we are working with around 50 of them,” Srivastava told Packaging South Asia.
Specialized inks aimed at the food & pharma segments
UFlex manufactures a range of toluene-free water-based inks meant for food packaging applications. “After the ban on toluene as per the Bureau of Indian Standards IS 15495: 2020, I can proudly say that all of UFlex’s businesses and converting companies are completely toluene-free now. Our Jammu plant is completely toluene-free, and our inks are compliant with UPA compliance and safety compliance,” Srivastava said.
The pharma sector is making a big turnaround, and in particular, the packaging is moving beyond foil-based applications. “There is a new generation of alu-alu foils, which require different kinds of laminate structures, and sometimes getting a good bond is a big challenge. We have developed PU inks for pharma applications. ACG Pharma is one of our customers, and we have been supplying them with polyolefin-based inks for alu-alu applications.”
“Our second offering is for laminating adhesives. Most of the pharma adhesives are being imported from Korea and other parts of the world. As part of the Make in India campaign and as an Indian company, we are ready to support the industry by sharing technical knowledge,” Srivastava said.
Cost wars
Srivastava says cutthroat price pressure has always been present in the inks segment. During the Covid-19 pandemic, prices shot up because of the disruption in the supply chain and raw material shortage. Getting good speed machines, good ink quality, good printing quality, and good dot transfer – became a big challenge for business owners.
“On the one hand, business owners are looking at the price per kg product, while on the other hand, they are also looking for peace of mind so that the ink runs flawlessly for hours and hours. Consistency and quality are non-negotiable – we at UFlex have very stringent measurements in terms of raw material selection, manufacturing processes, products, their stability, and shelf life. We are working in totality to offer complete, seamless performance,” he added.
According to Srivastava, price is not the only driving factor, good ink quality, and cost-effective performance are some of the challenges that his organization is overcoming as a leading ink manufacturer. At the end of the day, as packaging becomes safer, the inks are also getting safer. The kind of inks prevalent in the market a few years ago has completely changed. “We have already launched and commercialized water-based inks and I hope that there will be a lot of sustainable inks as the entire world will keep on changing,” he says.
“This event (PlastIndia) is happening almost after five years – a big turnaround cycle with huge crowds. I hope that the market is also opening up. People are looking at alternatives from China as a substitute for packaging suppliers. We see many visitors from Kenya and other African and Middle Eastern countries. With several clients in East Africa, South Africa, and West Africa. The African continent is a significant contributor to our business,” Srivastava concludes.