Two tanks placed several meters above the ground? Or the conversion of a complete formulation system for new products in the shortest possible time? Some customer inquiries appear to be unsolvable at first glance. But with the appropriate expertise, agility, and creativity, even these challenges can be overcome, as Janssen Vaccines Corporation and Syntegon have proven in their many years of cooperation.
Janssen Vaccines Corporation and Syntegon – a specialist in processing and packaging solutions for the pharmaceutical and food industries – look back on more than 10 years of highly successful business relations. The German Syntegon subsidiary Pharmatec has already implemented demanding projects at the site in Incheon, South Korea. Janssen Vaccines Corporation is part of Janssen Pharmaceutical Companies of Johnson & Johnson. In Korea, around 200 people work to treat, cure, stop, and prevent some of the most devastating and complex diseases — from heart disease, diabetes, and psoriasis to Alzheimer’s, HIV, Covid-19, and cancer.
Janssen and Pharmatec worked together for the first time as far back as 2009. Ever since, Pharmatec’s engineering and service team has traveled to Incheon regularly and has completed numerous further engineering projects and service assignments. In 2020, the production site in Korea took an important strategic step: to extend production to several new drug products, Janssen had to transfer processes from a European to its Korean site. As a long-term partner, Pharmatec was ready to support the customer with its technological and service expertise.
A highly customized system
The start of this long-term cooperation was the installation of a customized system. It ensures the manufacture and filling of two distinct products for the treatment of Hepatitis B and diabetes, as well as a pediatric vaccine. The installation consists of a formulation system, which mixes the products and transfers them to a storage tank located right before the Syntegon vial filling equipment. Further Syntegon components include two Cleaning-in-Place (CIP) systems, a pure water storage and distribution system, a distillation unit, and a pure steam generator. The distillation unit produces water, which is stored in Water for Injection (WFI) tanks and then distributed. The CIP systems are used to clean the equipment after a batch and before a new formulation.
The system is quite unique, both from a technological and a constructional perspective. It is situated on two floors, with four fixed tanks on the second floor and another slot for a mobile vessel on the first. In a dedicated room on the second floor, the product is formulated via two formulation and one buffer tank, as well as a vessel for aluminum gel. The latter is an important carrier substance required during formulation. Formulated products are transferred from floor two to floor one. The first-floor tank is used for the storage and recirculation of the final formulation right before filling. Recirculation is necessary for certain products to maintain formulation structure.
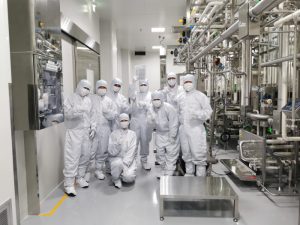
From modernization to manufacturing flexibility
A few years ago, however, Janssen had to replace its old first-floor tank. “Thanks to the immediate intervention by the Syntegon service team, we were able to keep production running – and much more,” Hae Eun Jeong, project engineer at Janssen says. In the wake of the patent expiration of its pediatric vaccine, Janssen had reoriented its production, adding multiple new products to its portfolio, essentially vaccines and parenterals such as monoclonal antibodies for cancer treatment. Given Janssen’s need for increasingly flexible manufacturing, the Pharmatec experts installed a solution that enabled Janssen to maintain overall production while easily switching between different formulation volumes. What started out as a modernization thus turned into a major opportunity for the project partners. “We realized that this was the right time to ramp up our flexible manufacturing readiness,” Hae Eun Jeong says.
Instead of a single tank on floor one, Janssen opted for two tanks that the company can flexibly use depending on desired manufacturing outputs: a 600-liter tank for large batches and a 150-liter variant for smaller production runs. Both containers can be easily connected to the vial filling station from Syntegon. Their location remains unchanged: just like the single replaced tank, the two new ones are situated approximately 2.5 meters above ground in Janssen’s clean room. Correspondingly, pumps, discharging, and further equipment had to be installed at that height. “We wanted to improve accessibility and decided to build a lifting column to move the 600- and 150-liter active ingredient tanks. Due to Syntegon’s service and engineering support, we mastered this uncommon challenge,” Hae Eun Jeong underlines.
Lifting two containers proved to be a challenging yet rewarding project for the Pharmatec engineers. “Often, customer requests sound unusual or even unsolvable at first thought. But in the end, you can fulfill them with creativity, spontaneity, and technical knowledge,” says Martin Jäger, Pharmatec’s senior manager, Sales Engineering, and project manager in the modernization process. In this specific case, a lift supplier was found who was willing to give the project a try and provided a solution that met Janssen’s requirements to the fullest.
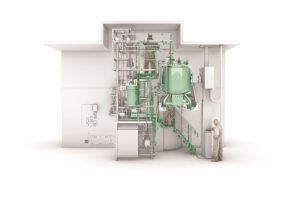
Single-use for higher process safety
Janssen did not limit its newly found flexibility to the clean room’s first floor. “Manufacturing readiness needs to play out in the entire system to be a real success,” Hae Eun Jeong emphasizes. Just like floor one, floor two saw an increase in versatility: together with the Syntegon engineers, Janssen implemented a new interface for single-use drug product bags that can be connected to the formulation system according to the product at hand. A third-party supplier provides the sterile bags, which Janssen’s staff can flexibly connect to the four tanks already in place via specific coupling bends on a so-called transfer panel – the heart of the system for connecting bags, tanks, and further equipment. “This hub not only allows us to easily connect various system components according to our needs. The single-use approach further adds to a sterile manufacturing environment and reduced cleaning efforts.”
For several months, the project team was on site for start-up and qualification – and did not lose any precious time. The entire flexible manufacturing project at Janssen’s South Korean site took half a year of engineering, followed by eight weeks of mechanical and electrical rebuilding, as well as qualification. Following some final technical touches, the system was fully qualified. Janssen now not only has the desired two tanks and a construction that makes it easy to lift them to the required height. Thanks to the overall system optimization, the pharmaceutical manufacturer can now run different batches simultaneously, achieving more output per shift and greater flexibility in drug product manufacturing. “The support from Pharmatec has enabled us to truly diversify our portfolio and to keep a firm foothold in a market that is prone to rapid change,” Hae Eun Jeong says.
Cooperation to continue
Right now, the project partners are working on crucial next steps. The Human-Machine-Interface (HMI) will receive an upgrade, and staff will be trained on the new and modernized equipment to ensure smooth operations from the very beginning. “The quality and agility of the team, as well as its willingness to provide practical solutions really kicked in,” says Hae Eun Jeong. “Our team and Syntegon’s share a strong bond, and I am very confident that we will continue our cooperation, also in the larger Johnson & Johnson network.”
(The article has been authored by Martin Jäger, project manager / senior manager, Sales Engineering, Pharmatec, a Syntegon Technology Company. Write to Martin at martin.jaeger2@syntegon.com)