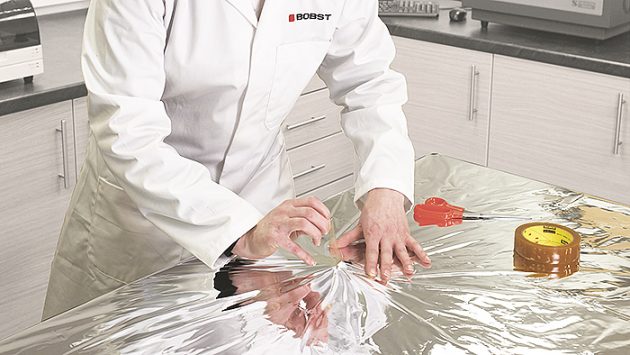
The past two years have been active growth periods for the Indian flexible packaging industry. While the pandemic seems to have spurred the overall growth of hygienically packed products, the investments in large film lines point to significant long-term growth for flexible packaging. However, sustainable laminate structures that are cost-effective are crucial to survival in the future. Although several approaches are discussed daily, the one that has found favor with many film manufacturers and flexible packaging converters is the use of vacuum metalized films.
The more than dozen film lines ordered by Indian companies in 2020, amounting to more than 20% of the order intake of the largest global manufacturer in that year, have begun installation this year. In addition, a large number of gravure and CI flexo presses and laminators were installed and commissioned in 2020. Significantly, more than a dozen vacuum metalizers were also commissioned in 2020, and most were from Bobst.
In the first eight months of the current year, more than a dozen vacuum metalizers are already on order, and the pace will likely continue. Therefore, it is safe to say that in the two calendar years of 2020 and 2021, the Indian market will absorb more than 30 vacuum metalizers. Driving this investment is the need to improve the oxygen and moisture barrier of a variety of films with a good deposition of metal and also to try and avoid the cost of an extra film layer or coating.
Of the Bobst Expert K5 vacuum metalizers that came last year and are already ordered this year, an extraordinary number (an estimated 90%) contain Bobst’s AluBond technology. Other manufacturers have also sold their vacuum metalizers into the Indian market with similar technologies for superior metal adhesion to film substrates.
A common problem in film structures for flexible packaging is poor metal adhesion due to de-lamination. Traditional metalization, even with plasma treatment, can result in poor metal to polymer substrate bonding. This produces de-lamination, which leads to packaging failure and results in product rejects and loss of reputation.
Developed initially for polyester films, AluBond is now increasingly used with BOPP and PE films to provide the oxygen and moisture barrier properties required, especially for food packaging that is more easily recyclable. We are familiar with many Indian companies that have invested in the technology, including Sparsh Industries, SRF and Constantia – all three which we have written about.
The problem is low surface energy on the metal side, contributing to poor lamination bonding. In addition, there is increasing demand in the industry for higher levels of metal adhesion on metalized film due to the need for more complex packaging structures, which requires a lamination peel strength suitable for functional needs. This attribute is easily tested using the standard tape test.
The AluBond metalizing process achieves high bonding strength on any substrate. It is an advanced metal adhesion technology that can achieve metal adhesion values of up to 5N/15mm. Moreover, the innovative approach has eliminated the need for chemically treated films.
How does Bobst AluBond work?
The Bobst AluBond process is an in-line hybrid coating technology incorporated in its Expert K5 vacuum metalizers. It promotes the chemical anchoring (chelation) of the first aluminum particles creating a metalizing seeding layer that provides superior bond strength properties. Very high adhesion is achieved when there are direct chemical bonds between the aluminum coating and the polymer surface. Increased chemical bonding by creating the seeding layer increases lamination bond strength and leads to high performance during lamination, extrusion, and coating processes hence preventing the failure of the packaging.
Increased metal adhesion and dyne level retention
AluBond has been shown to greatly increase metal bond strength and metal adhesion on the most commonly used substrates (PET, BOPP, CPP, and PE) during aluminum vacuum metallization. In addition, the process innovation also significantly increases dyne level retention, which translates in improved ink wettability during printing and enhances structure stability during lamination. Finally, the adhesion technology generates added value by extending surface energy stability on metalized films over a long period and may eliminate the need for an additional surface treatment boost such as a corona refresh before converting.