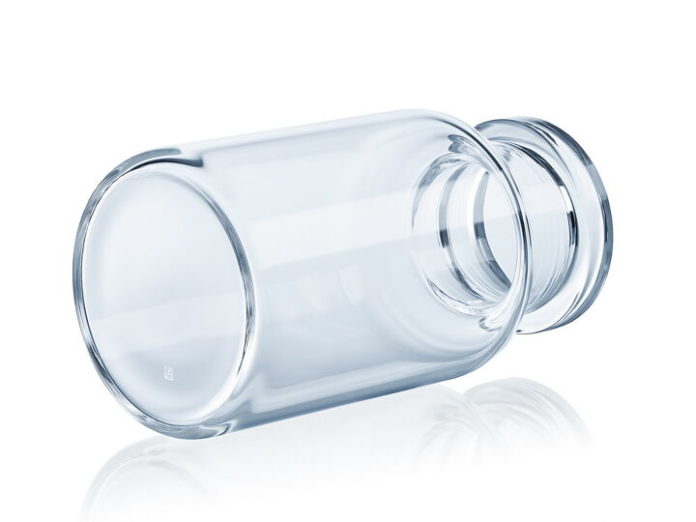
In light of the growing need for pharmaceutical packaging innovations and digitalization, the international technology group SCHOTT is introducing smart containers. The concept enables industry 4.0 for pharma manufacturers to unlock the power of machine vision and big data analytics on pharmaceutical filling lines. Each SCHOTT smart container is laser-marked with a unique identifier to create unprecedented traceability throughout the manufacturing process. The technology can be used to improve reject management and line clearance. Other applications include reducing the risk of a mix-up, optimizing lyophilization processes, and supporting container-based targeted recalls.
“SCHOTT smart containers enable control over pharmaceutical packaging at the most granular level available – the individual unit,” said Diana Löber, global product manager – Vials at SCHOTT. “We’re unlocking a new era in digitized pharmaceutical manufacturing toward real-time release and taking advantage of the latest developments in machine vision and data science.”

Each smart container is marked with a data matrix code that can be as small as 1 x 1 mm, which equals 14 x 14 dots. Developed according to ISO/IEC 16022, the numeric or alphanumeric machine-readable code contains 16 or 24 digits, leading to sextillions of possible individual unique numbers. For vials, the unique identifier is positioned at the bottom, hence eliminating the need to turn the container or install multiple cameras, as it would be the case if the code were placed on the body of the vial.
The code remains stable during the whole fill and finish process, including washing, autoclaving, and depyrogenation (removal of pyrogens from solution, most commonly from injectable pharmaceuticals) up to a temperature of 600°C. It resists abrasion and avoids the risk of particle contamination, a key advantage over solutions that need additional substances for the application of the code. Moreover, in contrast to engraving laser technologies, the data matrix code of smart container is applied via melting to maintain glass strength. By inextricably linking the code to the container at the earliest possible stage within the entire value chain, the concept offers an advantage over systems wherein the code is attached or adhered at a later stage.